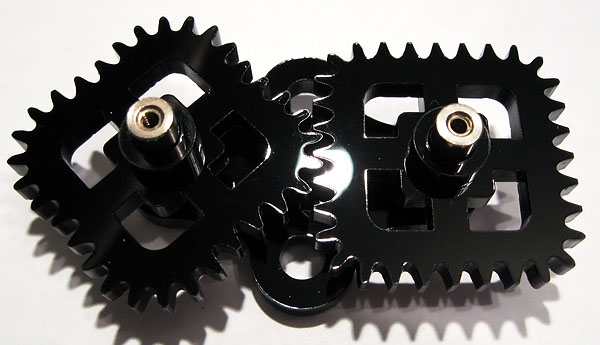
Non-circular gears.
Non circular gears are strange. When the topic of square gear trains appears in casual conversation, people tend to think a joke is being made, that it is 'impossible' to make a square gear that actually meshes properly. After being drawn into a vicious debate with a co-worker about the existence and plausibility of such gears, I realized I had no choice but to resort to an actual demonstration to sway his view. In the not-too distant past this would have been a virtual impossibility, at the very least I would have had to spend an indeterminate amount of time hunched over a scroll saw, trying to cut splintery wooden gear prototypes by hand. Fortunately, this is the pushbutton world of the 21st century, a Google search turns up dozens of laser / waterjet cutting services and MakerBots are squeezing out ABS plastic Darth Vader helmets in every good nerd's house this Christmas. And thus, a project was born...
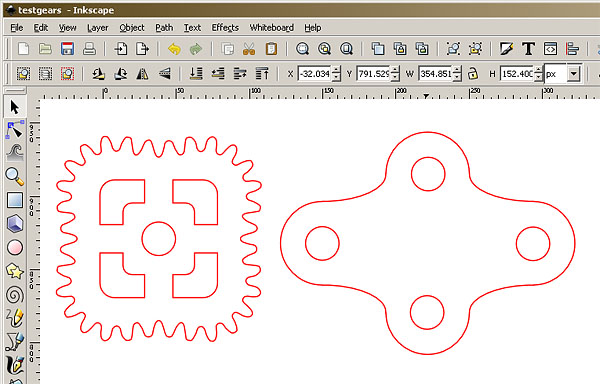
Gear layout design in Inkscape.
I chose to employ a laser-cutting service to make the gears, which necessitated the creation of a vector file which would be sent to the cutting service to make the actual part. I used Inkscape to make the vector file, which, like many free or open source programs of this sort, has a flaky non-standard interface that leaves you with the vague feeling you have stumbled into a parallel universe suffering from Casual Domain Shear; key combos and controls all behave slightly differently from the standards adopted by mainstream programs. That said, Inkscape is completely free, and can output vector files in the Encapsulated Postscript and SVG formats most cutting services will demand. Inkscape has a slick automatic gear tool that can generate standard circular gears with only a few mouse-clicks, but to create an outline for a square gear I was reduced to drawing each tooth by hand based on a photo of a non-circular gear I found on Google. Lasercutting puts a hard limit on just how small of a gear can be manufactured, the teeth of the gears pictured above are sized at about 1mm across the tip, any smaller and they would have been deformed by the heat from the cutting laser.
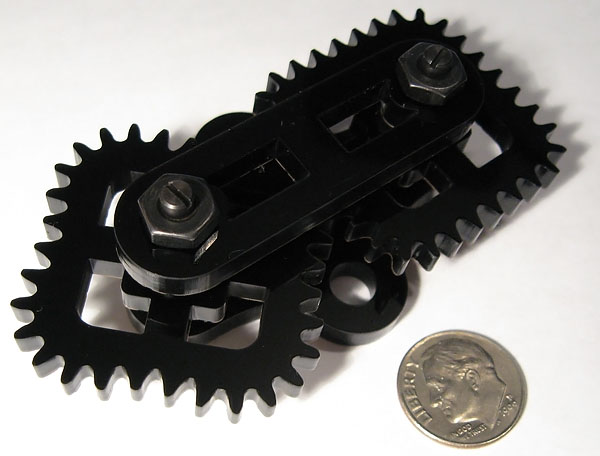
Non-circular gears, completed object.
And here is the finished product cut from 4mm acrylic. I placed small plastic cut bushings above and below each gear to prevent them from getting scuffed from rubbing against the supports. The bottom support has two extra tabs with mounting holes, which I included so I could bolt the entire device to a block of wood or something similar to make it easier to hold. 1/4 inch standoffs and machine screws from the local electronics store complete the device.
The square gears looked so lonely, sitting there on the shelf by themselves, that I made a matching set of triangular gears to go with them. With this set of gears I replaced the linear top spar with a curved one which made it easier to see the intersection of the gear's teeth.
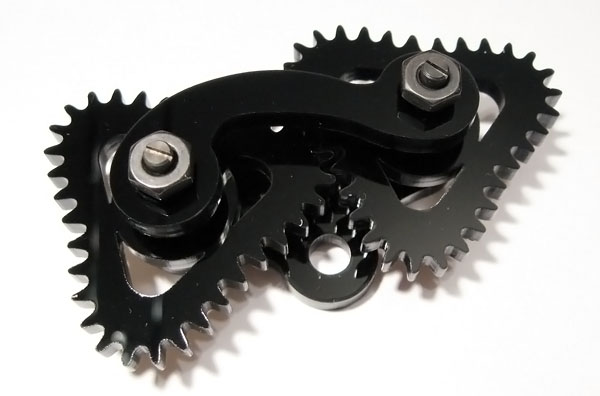
Triangular gears, completed object.